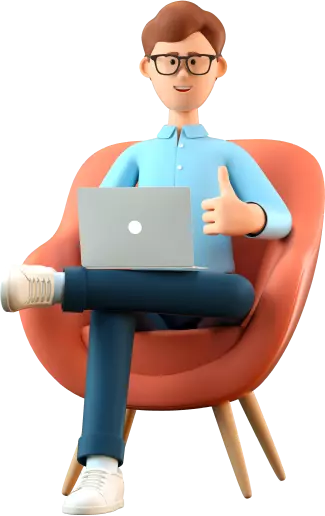
на первый
заказ
Дипломная работа на тему: Литературный обзор. Методы определения. Термохимический метод
Купить за 600 руб.Введение
В прокатных цехах российских предприятий в настоящее время работает около 240 методических нагревательных печей. До конца 60-х годов строили наиболее простые по конструкции и относительно дешевые толкательные печи. Когда они перестали удовлетворять требованиям прокатного производства, начался переход на печи с шагающим подом (мелкосортные и проволочные станы) и шагающими балками (листовые станы), которые хотя несколько сложнее и дороже, но лишены недостатков толкательных печей.[1]В конце 70-х годов строительство новых толкательных печей прекратилось, кроме достройки в существующих печных отделениях. К новым станам строили только печи с механизированным подом. До 80-х годов металлургия развивалась в основном экстенсивно: строились новые станы и новые печи, а старые оставались в прежнем состоянии. В 80-х годах началась реконструкция печей с выводом из строя устаревших прокатных станов; в 90-х годах она приостановилась. В результате наряду с современными печами с механизированным подом сохранились старые двух- и трехзонные печи без нижнего обогрева, перекатные, без рекуператоров, с керамическими и игольчатыми рекуператорами, с инжекционными горелками. Примерно 80 % печного парка составляют толкательные печи. Из них почти треть не имеет рекуператоров и столько же печей с керамическим рекуператором; печей с игольчатым - примерно 12 %. Средняя температура подогрева воздуха в игольчатых рекуператорах 200 "С, а в керамических - 340 °С. Печи с керамическими рекуператорами и инжекционными горелками составляют 10 % и столько же печей перекатных, с наклонным и лекальным подом. Средний срок службы этих печей более 40 лет. Конечно, в период реструктуризации металлургического производства многие из этих печей вместе со станами будут выведены из эксплуатации.
Методические печи предназначены для нагрева металла перед прокаткой и относятся к печам непрерывного действия. За время нагрева заготовки постепенно перемещаются через всю печь от входа к выходу.[2]
Методическая печь состоит из рабочего пространства, где происходит сжигание топлива и нагрев металла, и ряда систем: отопления, транспортировки заготовок, охлаждения элементов печи, управления тепловым режимом и др. Рассмотрим для пример! пятизонную топкатепьную методическую печь, изображение продольного разреза которой приведено на рис. 1. Наименование печи соответствует числу отапливаемых зон. Подлежащие нагреву заготовки подаются к загрузочному окну 1 печи с помощью рольганга загрузки 2 и заталкиваются и печь толкателем. Заготовки на рисунке не показаны, они лежат в печи вплотную одна к другой, соприкасаясь боковыми гранями. Поэтому при заталкивании в печь очередной заготовки все заготовки перемещаются вдоль печи. Одновременно из окна выдачи 3 на приемный рольганг 4 выдается нагретая заготовка.
Рабочее пространство печи разбито на зоны: методическую зону 5, верхнюю и нижнюю первые сварочные зоны 6 и 7, верхнюю и нижнюю вторые сварочные зоны и 9, томильную зону 10. Все зоны, кроме методической, оснащены горелками I1, в которых сжигается топливо (смешанный газ, природный газ, мазут).
Заготовки нагреваются постепенно (методично), перемешала, сначала через неотапливаемую методическую зону (зону предварительного нагрева). где температура сравнительно низкая, затем через сварочные (нагревательные) зоны с высокой температурой, где происходит быстрый нагрев металла, и томильную зону, в которой осуществляется томление - выравнивание температур по сечению заготовки. В методической и сварочных зонах заготовки перемещаются по водоохлаждаемым подовым трубам 12, я в томильной - по монолитной подине 13.
Продукты сгорания движутся в печи навстречу движению металла, отдавая ему значительную часть тепла (в последнее время разрабатываются методические печи, в которых направление движения продуктов совпадает в некоторых зонах с направлением движения металла, однако они не получили широкого распространения), Из методической зоны они поступают в рекуператор 14, где нагревают воздух, подаваемый в зоны для горения ( в некоторых методических печах в рекуператорах нагревают также и газ).
Далее продукты сгорания во многих современных методических печах подаются в котлы-утилизаторы, где часть их тепла используется для выработки пара, после чего они отводятся в дымовую трубу.
На рис. 1 изображена схема одного из возможных вариантов методической печи. Методические печи могут различаться числом отапливаемых зон, формой рабочего пространства, способами перемещения металла, подвода топлива и воздуха, сжигания топлива, а также по размерам и производительности, по виду нагреваемого металла, по типу обслуживаемых станов и ряду других признаков . Ниже рассматриваются в основном те особенности различных методических печей, которые влияют на создание систем автоматического управления нагревом металла в них.
Число отапливаемых зон в методической печи может быть равно 2, 3, 4, 5, 6, 7 н более. Двух зонные печи без томильной зоны применяют для нагрева тонких заготовок (до ОЛ-0,15 м). В многозонных печах участок с высокой температурой растянут на большую длину, что позволяет форсированно греть металл и обеспечивать высокую производительность. Каждая зона отопления оснащается локальными системами автоматического регулирования (САР) температуры и режима горения. С увеличением числа зон в печи соответственно увеличивается число локальных САР и управление распределением температурного режима по длине печи становится более гибким.
Методическая печь, схема которой изображена на рис. 1, имеет верхние и нижние зоны. В таких печах металл греется с двух сторон: сверху н снизу, что повышает равномерность нагрева заготовки по толщине. Недостатком таких печей является наличие в них водоохлаждаемых подовых труб, что приводит к появлению темных (холодных) пятен на заготовках в местах их контакта с трубами и к увеличению расхода топлива. Поэтому применяются также методические печи только с верхним обогревом. Обычно для верхних и нижних зон проектируют одинаковые САР температуры. Однако в нижних зонах хуже условия для измерения температуры. Поэтому, как правило, системы регулирования в них работают менее эффективно. Иногда для нижних зон приходится создавать специальные САР. рис1
Задачей этих систем является обеспечение экономичного сжигания топлива, достижение наилучших условий теплообмена факела с металлом и кладкой и поддержание в печи газовой атмосферы определенного состава. Указанные задачи решаются путем направленного изменения соотношения воздух-топливо (Со), автоматическая стабилизация которого позволяет улучшить качество нагрева металла, уменьшить удельный расход топлива, угар и окалинообразованне.
В печах с ннжекционными горелками происходит саморегулирование Со, требуемое значение которого устанавливают, изменяя при наладке положение воздушных клапанов перед горелками. Если при полностью открытых клапанах воздуха все же недостаточно, то уменьшают размеры газовых сопел или переходят на сжигание газа с пониженной теплотой сгорания.
В печах с дутьевыми горелками регулирование осуществляют путем принудительного изменения расхода воздуха при изменениях расхода топлива или Со (схемы с ведущим топливом). Гораздо реже встречаются схемы с ведущим воздухом. Поддержание заданного значения Со обеспечивают локальные системы регулирования, использующие в качестве входной информации непрерывно измеряемые расходы топлива и воздуха. Величину Со устанавливают с помощью выносного задатчика, отградуированного либо непосредственно в единицах Со (м3 /м3), либо в единицах коэффициента расхода воздуха, определяемого как отношение измеренного расхода воздуха к теоретическому, необходимому для полного сжигания измеренного расхода топлива.
При заметных отклонениях барометрического или избыточного давления и температуры топлива или воздуха от расчетных в показания расходомеров вводят соответствующую поправку для приведения к стандартным условиям . Обычно учитывают только отклонения температуры.
Динамика объекта регулирования, которым а данном случае является участок трубопровода между диафрагмой и регулирующим органом (Р.О.), аппроксимируемый с достаточной степенью точности звеном чистого запаздывания и апериодическим звеном первого порядка, характеризуется Т0= 0,2-0,8 и Та =0,6-1,5 с и зависит главным образом от расхода и емкости участка трубопровода, импульсных линий и датчиков. Коэффициент передачи по каналу расход-положение Р.О. определяется расходной характеристикой и исходным положением регулирующей поворотной заслонки и связан существенно нелинейной зависимостью с измеряемым расходом . Наличие значительных люфтов в сочленении Р.О. с И.М. обусловливает резкое отличие коэффициентов передачи по каналу расход-положение И.М. при малых и больших перемещениях последнего.
В таких условиях удовлетворительное качество регулирования достигается при использовании ПИ-регуляторов со сниженным коэффициентом передачи пропорциональной части или при использовании чистых И-регуляторов. Настройка регуляторов выполняется по известным методикам при расходах, равных 60 ... 80% от максимальных. Так как при малых расходах в системе регулирование появляется склонность к автоколебаниям, а при больших - процесс регулирования затягивается, необходимо изменение динамических настроек регулятора по мере изменения расхода. При значительном снижении расходов (ниже 30% от максимального) резко снижается точность их измерения, а следовательно, и регулирования Со. При дальнейшем снижении расходов расходомеры становятся практически нечувствительными, и ошибка в поддержании заданного значения Со может составить 100% и более. Кроме того, из-за резкого снижения скоростей истечения из горелок перемешивание топлива и воздуха становится недостаточным и качество сжигания топлива ухудшается. В этом случае целесообразно перейти на работу с повышенным Со, прекратив снижение расхода воздуха при достижении некоторого предельного значения, определяемого экспериментально для каждой Мин. '" Такой переход оправдан, так как резкое снижение расходов (тепловой нагрузки) осуществляют, как правило, чтобы быстро снизить температуру в рабочем пространстве. Работа с избытком воздуха только ускорит этот процесс. Увеличение угара компенсируется исключением опасности оплавления нагреваемого метала, При длительной работе с такой низкой тепловой нагрузкой целесообразно перейти на дистанционное управление температурой рабочего пространства и процессом горения, отключив ряд горелок в каждой зоне.
Качественное регулирование заданного значения Со по измеренным расходам даже при достаточно больших тепловых нагрузках еще не гарантирует экономимого сжигания топлива и постоянства состава продуктов горения внутри печи.
Неконтролируемые изменения теплоты сгорания топлива, особенно при отоплении смешанным газом, приводят к колебаниям действительного значения Со. которые могут достигать значительной величины. Для устранения этих колебаний в систему регулирования вводят импульс от калориметра, непрерывно измеряющего теплоту сгорания топлива.
Действительное количество воздуха, поступающего в печь, может отличатся от измеренного. Это отличие обусловлено потерями на участках воздухопроводу расположенных после диафрагмы, и подсосами в лечь холодного воздуха из окружающего пространства. Количество теряемого воздуха может быть ориентировочно оценено при теплотехнических испытаниях печи. Количество подсасываемого воздуха зависит от давления в печном пространстве и увеличивается при снижении тепловой нагрузки. Используя эту зависимость, можно сформировать корректирующей импульс, вызывающий снижение заданного значение Со в соответствии с уменьшением тепловой нагрузки (уменьшением расхода воздуха или топлива). Введение такого импульса, а также учет теряемого воздуха позволяют снизить влияние этих факторов, но не устранять его полностью. Кроме того, в принеси эксплуатации печи количество теряемого воздуха к зависимость между количеством подсасываемого воздуха и тепловой нагрузки меняются.
Достаточно точно о составе атмосферы печи (полноте сжигания топлива) можно судить по результатам анализа продуктов сгорания, отбираемых в конце печи, или для печей большой мощности в конце каждой зоны . По найденному содержанию О2, СО, Н2, СН4 и N2 может быть рассчитан действительный коэффициент расхода воздуха. Разность между рассчитанным и заданным значением явится корректирующим сигналом регулятору Со. Применение указанного способа требует обеспечения представительности проб продуктов сгорания, отбираемых для автоматического анализа, решения задачи очистки и охлаждения пробы, а также минимума запаздываний в импульсной линия и собственно газоанализаторе. Динамические характеристики современных автоматических газоанализаторов на порядок больше динамических характеристик объекта управления, что приводит при непосредственном регулировании Со по результатам анализа: к большим и знакопеременным динамическим погрешностям. Представительный импульс может быть сформирован только по большому количеству отдельных измерений и, характеризуя тенденцию изменения действительного значения Со, может использоваться в качестве корректирующего сигнала.
Если в печи осуществляется полное сжигание топлива, то достаточно контролировать только содержание О2 в продуктах горения . Такой анализ может быть выполнен с достаточным быстродействием и без применения сложных устройств отбора и подготовки пробы с помощью датчика с твердым электролитом (твёрдоэлектролитной ячейки), пропускающего ионы О2. Э.д.с., развиваемая дат" ком, зависит от его температуры и концентрация О2, максимальная чувствительность достигается, когда эта концентрация близка к нулю. Для датчика, выполненного из циркония, допустимая рабочая температура равна 2000°С, что позволяет располагать его в любом участке тракта отходящих газов, а также и непосредственно в рабочем пространстве печи, вблизи факела. В первом случае температуру, а следовательно, и градировочную характеристику датчика стабилизируют с помощью дополнительного электроподогрева по сигналу ТП, смонтированной в одном корпусе с датчиком. Во втором случае датчик одновременно используется для стабилизации температуры рабочего пространства (его ТП подключается на вход регулятора топлива) и для регулирования Со. При этом регулирование Со начинается после того, как температура датчика и рабочего пространства достигает заданного значения.
Малые размеры и высокое быстродействие датчика с твердым электролитом позволяют осуществить контроль качества сжигания топлива не только в каждой зоне, но и в каждой горелке н значительно расширить диапазон работы системы регулирования Со, одновременно упрощая эту систему.
Чтобы уменьшить кратковременные колебания Со, связанные с запаздыванием показаний расходомеров или с прекращением регулирования, вызванным отклонением температуры датчика от заданного значения, в систему может быть введен импульс от исполнительного механизма (И.М.), перемещающего регулирующим органом (Р.О.) на трубопроводе топлива. Подключенный через дифференциатор к регулятору расхода воздуха этот импульс обеспечивает одновременный поворот обоих Р.О., что приведет к одновременному изменению расходов топлива и воздуха. Оставшееся отклоните Со от заданного значения будет устранено по сигналам расходомеров или сигналу вышедшего на заданную температуру датчика с твердым электролитом.
Управление сжиганием топлива может выть осуществлено также с помощью экстремальных систем регулирования, в которых в результате непрерывного поиска определяется значение Со, обеспечивающее максимальную при данном расходе
Рис2
топлива температуру в области, контролируемой датчиком. На рис. 2 показана принципиальная схема локальной системы, позволяющей реализовать описанные выше способы управления режимом сжигания топлива.
Измерение расхода воздуха выполняется с помощью диафрагмы/ и дифманометра 1 (ДМ-Э). Поправка к показаниям расходомера формируется с помощью ТП 2(ТХА-151), нормирующего преобразователя 3 (Ш-72) и блока нелинейного преобразования 4 (БНП). Вычисление расхода воздуха, приведенного к стандартным условиям, выполняется блоком умножения 5 (БВО), сигнализация достижения минимального расхода, еще обеспечивающего устойчивую работу горелок - блоком б (БСГ).
Величина заданного Со устанавливается на выносном задатчике 7 (РЗД), выходной сигнал которого суммируется с сигналами коррекции в сумматоре блока 8 (БВО). Там же осуществляется деление вычисленного расхода воздуха на скорректированное значение Со. Расход топлива измеряется с помощью
диафрагмы 11 и дифманометра 9 (ДМ-Э) . Для формирования импульса, уменьшающего запаздывание, служат датчик положения вала И.М. 10 (МЭО 25/100) при Р.О. IV
и дифференциатор 11 (ЭД). С помощью преобразователя 12 (БНП) реализуется зависимость, в соответствии с которой изменяются параметры динамической настройки регулятора 13 (РБИ-3) при изменении тепловой нагрузки. Для перехода на дистанционное управление служит блок 14 (БРУ-У), соединенный через пускатель 75 (ПРБ-74) с двигателем 16 (МЭО 25/100), перемещающим Р.О. III.
Теплота сгорания топлива контролируется датчиком 17 (КГ-7093.01), корректирующий импульс формируется во вторичном приборе 18 (КГ-7093.02). Коррекция задания при изменении тепловой нагрузки осуществляется с помощью блока 19 (БНП). Корректирующий импульс по содержанию О^ в продуктах сгорания зоны печи V может поступать в зависимости от положения переключателя 111 либо от комплекта, состоящего из устройства отбора и подготовки пробы 20, автоматического газового анализатора 21 (МН-5106) и интегратора 22 (БПИ), либо от датчика с твердым электролитом 23 в комплекте с преобразователем 24 (Циркон), либо, наконец, от датчика 25, расположенного в пламени горелки VI, и преобразователя 26. В последнем случае ТП датчика 25 через преобразователь 27 подключается на вход регулятора температуры рабочего пространства. Заданная концентрация О2 в месте установки соответствующего датчика вводится с помощью задатчика 28 (РЗД).
Экстремальное регулирование выполняется с помощью датчика 29 (ТЕРА-50) и экстремального регулятора 30 (ЭРБ), подключаемого через ключи 111 и П2 к сумматору блока 8 или через ключ П2 непосредственно к блоку 14 в зависимости от типа выходного сигнала регулятора 30.
При переводе переключателя Я в положение а, Ъ и d элементы схемы 1, 2, 3, 4, 5, 6, 7, делитель блока 8, элементы 9, 17, 18, 19, 20, 21 и 22 непосредственно в регулировании могут не участвовать.
Наладка системы на объекте состоит в определении исходных параметров динамической настройки регулятора 13, выполняемом по известным методикам на основании кривой разгона, снятой при тепловой нагрузке порядка 70-80% от максимальной; настройке блока 12 для обеспечения постоянного характера переходного процесса в широком диапазоне изменения тепловой нагрузки и настройке блока 19 по результатам газового анализа для обеспечения постоянного состава атмосферы печи. Все остальные элементы проходят предварительную приборную наладку в соответствии с инструкциями по их эксплуатации до установки на объекте и периодически поверяются в дальнейшем.
При. сжигании топлива одна из главных проблем - обеспечение оптимального соотношения между количеством подаваемых в топку топлива и воздуха.
Для каждой конкретной установки существует оптимальный избыток воздуха, который соответствует наиболее экономичному протеканию процесса сжигания. Недостаток воздуха при горении способствует образованию токсичных продуктов неполного сгорания, вызывает перерасход топлива. Избыток воздуха также приводит к перерасходу топлива на нагрев лишнего воздуха в составе отходящих газов. В обоих случаях сжигание топлива сопровождается повышенным выбросом в атмосферу высокотоксичных оксидов азота. Одним из наиболее достоверных способов определения избытка воздуха является анализ газовой смеси, покидающей камеру сгорания, а именно определение концентрации кислорода в топочных газах. В соответствии с "Инструкцией по проектированию и безопасной эксплуатации факельных установок для горючих газов и паров" должен осуществляться автоматический контроль за концентрацией кислорода в газах, сбрасываемых на факел. Концентрация кислорода в такой газовой смеси не должна превышать ≈2 % (об.).
Оглавление
- Введение 2- Литературный обзор
- Методы определения
- Термохимический метод
- Газоанализаторы ВТИ-2, ГХЛ-1, ГХЛ-2
- Электрохимические методы
- Полярографический метод
- Кулонометричесий метод
- Потенциометрический метод
- Использование твердых электролитов
- Автоматический анализатор кислорода 151ЭХО2
- Использование топливных элементов
- Оптические методы
- Оптико-акустические газоанализаторы
- Macс-спектрометрический метод
- Магнитные методы
- Термомагнитный метод
- Прибор Газоанализатор АГ0011
- Магнитопневматический метод
- Использование полупроводниковых чувствительных элементов
- Хроматографический метод
- Метод прямого измерения поглощения оптико-абсорбционный метод
- Основы метода
- Общие принципы и закономерности
- Основные способы повышения чувствительности и селективности
- Аппаратура
- Источники зондирующего излучения
- Приемники излучения
- Схемы абсорбционных газоанализаторов
- Формула изобретения патента 2109269
- Газоанализатор ПЭМ-2М
- Автоматизированный стационарный пост контроля АСПК
Список литературы
- Для решения разнообразных задач в абсорбционных газоанализаторах используют различные источники зондирующего излучения: газоразрядные, тепловые, когерентные. По характеру излучения их можно разделить на источники сплошного, линейчатого и монохроматического излучения в УФ-, видимом и ИК- спектральном диапазонах.- Тепловые источники характеризуются сплошным спектром излучения в ИК диапазоне, высокой стабильностью излучаемой мощности, малым потреблением энергии и большими сроками эксплуатации. Используют несколько разновидностей таких источников.
- Глобар, представляющий собой стержень из карбида кремния; рабочая температура 1300 К;.
- Штифт Нернста, представляющий собой стержень, содержа- щий смесь оксидов циркония, тория, иттрия; обычная рабочая температура 1700 К;.
- Лампы накаливания с вольфрамовой или нихромовой спиралью, нагретой до 1000-1100 К, излучающие в видимой и ближней ИК-областях спектра.
или зарегистрироваться
в сервисе
удобным
способом
вы получите ссылку
на скачивание
к нам за прошлый год