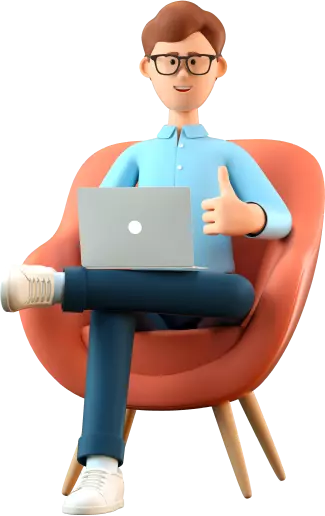
на первый
заказ
Дипломная работа на тему: Металлургическое производство. Производство меди. Разработка технологического процесса получения
Купить за 600 руб.Введение
Медь в промышленной классификации металлов образует совместно со свинцом, цинком и оловом группу основных тяжелых цветных металлов. К этой же группе под названием младшие (малые) относятся также висмут, сурьма, ртуть, кадмий, кобальт и мышьяк.История развития металлургии меди. Медь относится к числу восьми (Сu, Аu, Аg, Sn, Рb, Нg, Fе, и Sb) известных с древнейших времен металлов. Использованию меди способствовало то, что медь встречается в свободном состоянии в виде самородков. Масса наиболее крупного из известных самородков меди составляла около 800 т. Поскольку кислородные соединения меди легко восстанавливаются, а металлическая медь имеет сравнительно невысокую температуру плавления (1083 °С), древние мастера научились плавить медь. Вероятнее всего это произошло в процессе добычи самородной меди на рудниках.
Научились также выплавлять медь из богатых, отобранных вручную окисленных руд. Вначале плавку проводили, загружая на раскаленные угли куски руды. Затем стали делать кучи, складывая послойно дрова и руду. Позднее слон дров и руды начали помещать в ямы, подавая воздух для горения топлива по деревянным трубкам, заложенным в борта ямы. Полученный в яме слиток (крицу) меди по окончании плавки вынимали и проковывали.
По мере роста потребности в металле возникла необходимость увеличить выплавку меди за счет увеличения производительности плавильных устройств. Для этого начали увеличивать объем ям, выкладывая их борта из камня, а затем и из огнеупорного кирпича. Высоту стен постепенно увеличивали, что привело к появлению первых металлургических печей с вертикальным рабочим пространством. Такие печи являлись прототипом шахтных печей; они получили название домниц. Домницы в отличие от ям выдавали медь и получающийся шлак в жидком виде.
Роль меди в становлении человеческого общества и развитии его материальной культуры исключительно велика, недаром целые исторические эпохи развития человечества получили название "медный век" и "бронзовый век".
Изделия меди и бронзы были найдены при археологических раскопках в Египте, Малой Азии, Палестине, Мессопотамии и в Центральной Европе.
В глубокую древность уходит начало производства меди и на территории нашей страны. Искусными металлургами были скифы. Получило развитие производство меди в государстве Урарту на территории современной Армении. Оно снабжало медью Ассирию, Вавилон и древнюю Персию.
Кустарное производство меди было широко распространено в Киевской Руси и Великом Новгороде (по реке Цильме).
Первый медеплавильный завод на территории княжеской Руси был построен в 1640 г. стольником Стрешневым у Пыскорского монастыря в районе г. Соликамска. Упоминается также о постройке в 1669 г. медного завода в Олонецкой губернии.
Большое развитие медная промышленность России получила в начале XVIII в. По инициативе Петра Первого, который всячески поощрял развитие горного дела, в те времена на Урале было построено 29 медеплавильных заводов. Частным предпринимателям (Демидовы, Строгановы) для постройки горнопромышленных предприятий выдавали денежные средства, выделяли огромные участки земли. Наряду с частными строились также и казенные заводы. Многие из них по тому времени имели передовую технику, в частности широко использовали водяной привод. Россия заняла в XVIII в. первое место в мире по производству меди. Поставляемая во многие страны медь отличалась высоким качеством.
В XIX в. и начале XX в. Россия постепенно утратила свое ведущее положение по производству меди. Многие рудники и предприятия были отданы в концессии иностранным фирмам. Даже мизерные потребности в меди отсталой царской России удовлетворялись примерно на 70%. Во время первой мировой, а затем гражданской войн медная промышленность пришла в полный упадок. Рудники были затоплены, заводы остановлены и частично разрушены.
Высокими темпами развивается в последние годы медная промышленность в ряде капиталистических и развивающихся стран. Добыча и переработка медных руд осуществляется фактически на всех континентах земного шара.
После окончания второй мировой войны стала очень бурно развиваться медная промышленность Японии и ФРГ, несмотря на то, что эти страны практически не имеют собственных запасов сырья. Япония, производившая до войны всего 80 тыс. т меди, увеличила выпуск рафинированной меди более чем до 1 млн. т и заняла второе место в капиталистическом мире. Необходимость увеличения собственного производства меди в этой стране диктуется общими задачами развития промышленности и является ярким подтверждением роли меди в современном техническом прогрессе.
Физико-химические свойства меди и области её применения. В Периодической системе элементов Д.И. Менделеева медь расположена в I группе. Как элемент I группы медь при высоких температурах преимущественно одновалентна, однако ее наиболее распространенным в природе и более устойчивым при низких температурах является двухвалентное состояние.
Ниже приведены важнейшие физико-химические свойства меди:
Порядковый номер 29
Атомная масса 63,546
Конфигурация электронной оболочки 3d№є4s№
Потенциал ионизации, эВ:
Первый 7,72
Второй 20,29
Третий 36,83
Ионный радиус, м 10ˉ№є 0,80
Температура плавления, єС 1083
Температура кипения, єС 2310
Плотность, кг/мi:
При 20 єС 8940
В жидком состоянии 7960
Скрытая теплота плавления, кДж/кг 213,7
Давление пара, Па (1080єC) 0,113
Удельная теплоёмкость при 20 єС, кДж/ (кг град) 0,3808
Теплопроводность при 20 єС, Дж/ (см * с * град) 3,846
Удельное электрическое сопротивление при 18 єС,
Ом * м * 10ˉ№є 1,78
Нормальный потенциал, В +0,34
Электрохимический эквивалент, г/ (А * ч) 1,186
Медь является мягким, вязким и ковким металлом красного цвета, легко прокатывающимся в тонкие листы. По электропроводности она уступает только серебру.
В химическом отношении медь - малоактивный металл, хотя и соединяется непосредственно с кислородом, серой, галогенами и некоторыми другими элементами.
При обычной температуре сухой воздух и влага в отдельности не действуют на медь, но во влажном воздухе, содержащем СО2, медь покрывается защитной зеленой пленкой основного карбоната [CuСОз - Сu (ОН) 2], являющегося ядовитым веществом.
В ряду напряжений медь располагается правее водорода - её нормальный потенциал равен +0,34 В. Поэтому в растворах таких кислот, как соляная и серная, в отсутствие окислителя медь не растворяется. Однако в присутствии окислителя и в кислотах, одновременно являющихся окислителями (например, азотная или горячая концентрированная серная), медь растворяется легко.
В присутствии кислорода и при нагревании медь хорошо растворяется в аммиаке, образуя устойчивые комплексные соединения
Сu (NH3) C03 и Сu2 (МН3) 4СОз.
При температурах красного каления медь окисляется с образованием оксида СuО, который при 1000-1100°С полностью диссоциирует по реакции: 4СuО= 2Cu2O + О2.
Оба оксида меди легко восстанавливаются при температуре около 450 °С и малой концентрации восстановителя.
С серой медь может образовывать два сульфида: сернистую (CuS) и полусернистую (Cu2S) медь. Сернистая медь устойчива лишь при температурах ниже 507 °С. При более высоких температурах она разлагается на полусернистую медь и элементарную серу:
Таким образом, при температурах пирометаллургических процессов из оксидов и сульфидов фактически могут существовать только Си2О и Cu2S, в которых медь одновалентна.
Медь и ее сульфид являются хорошими коллекторами (растворителями) золота и серебра, что делает возможным высокое попутное извлечение благородных металлов при производстве меди.
Кроме благородных металлов, медь способна сплавляться со многими другими металлами, образуя многочисленные сплавы.
Ниже приводится приблизительный состав некоторых сплавовна основе меди,%*: бронза (обычная) - 90 Си, 10 Sn; латунь (обычная) - 70 Сu, 30 Zn; мельхиор - 68 Сu, 30 Ni, I Мn, I Fе; нейзильбер - 65 Сu,20 Zn, 15 Ni; константан - 59 Сu, 40 Ni, I Мn. Для изготовления украшений пригоден золотистый сплав, содержащий,%: 85 Сu, 12 Zn, 2 Sn.
Перечисленные выше характерные свойства меди обусловливают многочисленные области ее применения. Основными потребителями меди и ее соединений являются:
1) электротехника и электроника (провода, кабели, обмотки электродвигателей, токопроводящие шины, детали радиоэлектронных приборов, печатные схемы и др.);
2) машиностроение (теплообменники, опреснительные установки и др.);
3) транспорт (детали и узлы железнодорожных вагонов, автомобилей, самолетов, морских и речных судов, тракторов и др.);
4) магнитогидродинамические генераторы;
5) ракетная техника;
6) строительные материалы (кровельные листы, детали декоративных архитектурных украшений);
7) химическая промышленность (производство солей, красок, катализаторов, ядохимикатов и др.);
8) изделия и приборы бытового назначения;
9) сельское хозяйство (для защиты растений от болезней и вредителей, например медный купорос CuSO4 - 5Н2О).
Для промышленно развитых стран потребление меди характеризуется следующими примерными цифрами,% от общего потребления:
Электротехника и электроника 45 - 50
Транспорт 5 - 10
Машиностроение 10 - 15
Строительные материалы 8 - 10
Химическая промышленность 3 - 6
Прочие потребители До 10
Медные руды. Кларк меди, т.е. ее содержание в земной коре, равен 0,01%. Однако, несмотря на низкое содержание в земной коре, она образует многочисленные месторождения руд - естественные скопления рудных медных минералов. Характерным для меди является наличие в природе руд всех четырех рассмотренных выше типов.
Известно более 250 медных минералов. Большинство из них встречаются сравнительно редко, некоторые представляют собой драгоценные камни. К наиболее распространенным медным минералам, имеющим промышленное значение при получении меди, относятся прежде всего соединения меди с серой и кислородом. Наибольшее количество меди в земной коре (около 80%) входит в состав сернистых соединений. Ниже приведены важнейшие сульфидные минералы меди:
Минерал Сu%
Ковеллин CuS 66,5
Халькозин Cu2S 79,9
Халькопирит CuFeS2 34,6
Борнит Cu5FeS4 63,3
Кубанит CuFe2S3 23,5
Талнахит CuFeS2 36 - 34,6
Кроме того, довольно распространены медно-мышьяковистые (энаргит Cu3AsS4) и медно-сурьмянистые (тетраэдрит Сu3SbS3) минералы.
Сульфидные медные минералы имеют как гидротермальное, так и магматическое происхождение. При высоких температурах и давлениях вода, выделяющаяся при застывании магмы, наряду с сульфидами меди растворяет сульфиды, селениды и теллуриды многих других металлов и прежде всего железа, цинка, свинца, мышьяка и сурьмы. В растворе содержатся также благородные металлы, висмут и редкие металлы. При охлаждении термальных вод из них выкристаллизовывается целый комплекс ценных минералов: халькопирит CuFeS2, сфалерит ZnS, галенит PbS.
Основными компонентами пустой породы являются пирит FeS2 и кварц. Соотношение между ценными минералами может меняться в широких пределах. Совместная кристаллизация минералов, особенно если она протекала сравнительно быстро, часто приводит к очень тонкому их прорастанию, что крайне затрудняет разделение ценных минералов при обогащении. Поскольку температура кристаллизации различных минералов неодинакова, состав руды меняется по глубине месторождения. Меняются также стехиометрический состав однотипных минералов и содержание в них примесей.
Магматические месторождения, содержащие медь, образуются при кристаллизации ультраосновных пород. В этих месторождениях важнейшими спутниками меди являются никель, кобальт, платиновые металлы. Железо кристаллизуется в виде пирротина Fе (1-x) S, никель в основном в виде пентландита (Fе, Ni) S, но частично он может входить изоморфно и в состав пирротинов. Таким образом, и в магматических месторождениях медь встречается в комплексе со многими другими ценными элементами.
В природных условиях первичные сульфидные минералы могут подвергаться воздействию атмосферных агентов (кислорода, СO2, воды) и претерпевать изменения (выветриваться). Очень часто ковеллин и халькозин являются продуктом превращения первичных минералов. Более глубокое превращение приводит к образованию кислородных соединений меди. Ниже приведены основные минералы меди окисленных руд:
Минерал Сu%
Малахит СuСO3- Сu (ОН) 2 57,4
Азурит 2СuСО3 - Сu (ОН) 2 55,1
Куприт Сu2О 88,8
Тенорит (мелаконит) СuО 79,9
Халькантит CuSO4 - 5Н2О 25,5
Хризоколла CuSiO3 - 2Н2О 36,2
Диоптаз CuSiOs - Н2О 40,3
Вследствие низкого содержания меди и комплексного характера медных руд в большинстве случаев их непосредственная металлургическая переработка невыгодна, поэтому их предварительно подвергают, как правило, селективному флотационному обогащению.
При обогащении медных руд основным продуктом являются медные концентраты, содержащие до 55% меди (чаще от 10 до 30%). Извлечение меди в концентраты при флотации колеблется от 80 до 95%. Кроме медных, при обогащении руд часто получают пиритные концентраты и концентраты ряда других цветных металлов (цинковый, молибденовый и т.д.). Отходами обогащения являются отвальные хвосты.
Флотационные концентраты представляют собой тонкие порошки с частицами крупностью менее 74 мкм и влажностью 8-10%.
В металлургии меди роль предварительного обогащения очень велика. От содержания ценного компонента в перерабатываемом сырье зависят производительность металлургических агрегатов, расход топлива, электроэнергии и вспомогательных материалов, трудовые затраты, потери извлекаемых компонентов и в конечном итоге себестоимость готовой продукции.
Предварительное обогащение рудного сырья, значительно более дешевое, чем непосредственная металлургическая переработка, обеспечивает:
1) снижение затрат на последующие металлургические операции и себестоимости конечного продукта в первую очередь за счет сокращения объема перерабатываемых материалов;
2) возможность переработки бедных руд, непригодных для прямой металлургической переработки, т.е. расширение запасов природного сырья;
3) в ряде случаев повышение комплексности использования исходного сырья за счет выделения ценных компонентов в отдельные концентраты, пригодные для дальнейшей самостоятельной металлургической переработки.
Медные руды и получаемые при их обогащении концентраты имеют одинаковый минералогический состав и отличаются лишь количественными соотношениями между различными минералами.
Следовательно, физико-химические основы их металлургической переработки будут совершенно одинаковы.
Способы получения меди из рудного сырья. Переработку медного сырья можно проводить с использованием как пиро-, так и гидрометаллургических процессов. В промышленной практике металлурги имеют дело фактически с комбинированными технологическими схемами, включающими обе разновидности металлургических методов, как правило, с преобладанием одной из них, что и определяет в конечном итоге наименование технологии.
За рубежом в настоящее время пирометаллургическим способом производится около 85% от общего выпуска меди.
Таким образом, переработку медного рудного сырья в основном производят пирометаллургическими процессами.
К числу пирометаллургических процессов, применяемых при производстве меди, относятся окислительный обжиг, различные виды плавок (на штейн, восстановительные, рафинировочные), конвертирование штейнов и в ряде случаев возгоночные процессы. Типичными гидрометаллургическими процессами являются выщелачивание, очистка растворов от примесей, осаждение металлов из растворов (цементация, электролиз и др.), а также электролитическое рафинирование меди.
С учетом разновидностей перерабатываемых медных руд в настоящее время в промышленности используют три принципиальные пирометаллургические схемы.
Пирометаллургическую переработку сульфидных медных руд и концентратов можно вести двумя путями. Первый путь предусматривает полное окисление всей серы перерабатываемого сырья с помощью предварительного окислительного обжига (обжиг "намертво") при одновременном переводе меди и железа в оксидную форму:
Продукт обжига (огарок) далее подвергают селективному восстановлению при полном расплавлении материала - восстановительной плавке. При этом медь восстанавливается до металлического состояния, а железо - в основном до вюстита. Оксиды железа совместно с пустой породой руды и оксидами флюсов образуют шлак, который удаляют в отвал. Процесс восстановления описывается следующими основными реакциями:
Сu2О + СО = 2Сu - СО2, (3)
Fe203 + СО = 2FeO + С02, (4)
FeO+СО=Fе+CO2. (5)
Такой прием получения меди кажется наиболее простым и естественным. Именно поэтому он, по существу, был единственным способом переработки медных руд в XVIII и XIX вв. Однако целый ряд существенных недостатков восстановительной плавки заставил отказаться от ее применения. В настоящее время процесс, близкий к восстановительной плавке, используется лишь для переработки вторичного медного сырья.
Важнейшими недостатками этого метода являются:
1. При плавке получается очень грязная (черная) медь, содержащая до 20% железа и других примесей. Это, как известно из теории пирометаллургических процессов, объясняется облегченными условиями восстановления железа в присутствии расплавленной меди. Рафинирование черной меди от большого количества примесей является очень сложным и дорогим и связано, кроме того, с большими потерями меди.
2. Шлаки, находящиеся в равновесии с металлической медью, получаются очень богатыми, что снижает извлечение меди в товарную продукцию.
3. Плавка осуществляется с большим расходом (до 20% от массы шихты) дефицитного и дорогого кокса.
Второй путь, характерный для современной пирометаллургии меди, предусматривает на промежуточной стадии технологии плавку на штейн (сплав, главным образом, сульфидов меди и железа) с последующей его переработкой на черновую медь. Пустая порода при этом переходит в шлак. Плавку на штейн можно вести в окислительной, нейтральной или восстановительной атмосфере. В I условиях окислительной плавки можно получать штейны любого заданного состава. В этом случае преимущественно будут окисляться сульфиды железа с последующим ошлакованием его оксида кремнеземом по реакции
2FeS + ЗО2 + SiO2 = 2FeO - SiO2 + 2SO2. (6)
При плавке на штейн в нейтральной или восстановительной атмосфере регулировать степень десульфуризации невозможно и содержание меди в штейнах будет незначительно отличаться от ее содержания в исходной шихте. По этой причине для получения более богатых по содержанию меди штейнов при переработке бедных концентратов иногда целесообразно предварительно удалить часть серы путем окислительного обжига, осуществляемого без расплавления материала при 800-900 °С.
Дальнейшую переработку штейнов с целью получения из них металлургической меди осуществляют путем их окисления в жидком состоянии.
При этом вследствие большего сродства железа к кислороду сначала окисляется сульфид железа по реакции (6). После окисления всего железа и удаления получившегося шлака окисляют сульфид меди по суммарной реакции:
Технология, включающая плавку на штейн, позволяет получать более чистый металл, содержащий 97,5-99,5% Сu. Такую медь называют черновой. Рафинирование черновой меди по сравнению с черной значительно упрощается и удешевляется.
В последние годы в металлургии сульфидного сырья все большее развитие получают автогенные процессы, осуществляемые за счет тепла от окисления сульфидов при использовании подогретого дутья и дутья, обогащенного кислородом. В этих процессах, являющихся окислительными плавками, в одной операции совмещаются процессы обжига и плавки на штейн.
Современная пирометаллургия меди, несмотря на принципиальную общность используемых различными предприятиями технологических схем, предусматривает несколько вариантов (1-IV) ее практического осуществления (рис).
Как следует из рис., технология получения черновой меди характеризуется многостадийностью (за исключением варианта IV, предусматривающего непосредственную плавку концентратов на черновую медь).
В каждой из последовательно проводимых технологических операций постепенно повышают концентрацию меди в основном металлсодержащем продукте за счет отделения пустой породы и сопутствующих элементов, главным образом железа и серы. На практике удаление железа и серы осуществляют за счет их окисления в три (обжиг, плавка, конвертирование), в две (плавка, конвертирование) или в одну стадию.
Наиболее распространенная до настоящего времени технология предусматривает (см. рис) обязательное использование следующих металлургических процессов: плавка на штейн, конвертирование медного штейна, огневое и электролитическое рафинирование меди. В ряде случаев перед плавкой на штейн проводят предварительный окислительный обжиг сульфидного сырья.
Плавку на штейн медных руд и концентратов - основной технологический процесс - можно проводить практически любым видом рудных плавок. В современной металлургии меди для ее осуществления используют отражательные, руднотермические (электрические) и шахтные печи, а также автогенные процессы нескольких разновидностей.
Что же касается месторождений меди на Украине, то их можно назвать очень бедными, по сколько залежей меди на территории нашей страны практически нету. Вот только незначительная часть месторождений медных руд расположена на Волыне и Подолье. Причём слой проникновения этих залежей колеблется в приделах 0,2 - 0,5 м. Поэтому сырьевая база меди мала.
Оглавление
- Металлургическое производство- Производство меди
- Разработка технологического процесса получения отливки методом литья в разовые литейные формы
- Для детали необходимо получить заготовку методом литья в разовую песчано-глинистую форму
- Разработка чертежа модельно литейных указаний
- Разработка чертежа модели, стержня и стержневого ящика
- Разработать технологический процесс получения поковки
- Исходные данные
- Определение припусков и разработка чертежа поковки
- Определение массы, размеров и вида исходной заготовки
- Определение технико-экономических показателей разработанной поковки
- Определить температурный режим ковки и тип нагревательного устройства
- Выбор оборудования для формообразования поковки
- Разработка технологической схемы формообразования поковки
- Устройство камерной печи
- Основные операции ковки и применяемые инструменты
- борудование для ковки
- Исходные данные
- Технологические методы обработки поверхностей 1, 2, 3, применяемое оборудование, режущий инструмент и приспособления для закрепления заготовки
- Схема обработки поверхности
- Расчёт режимов резания для обработки поверхности
- Эскиз режущего инструмента, применяемого при обработке поверхности
или зарегистрироваться
в сервисе
удобным
способом
вы получите ссылку
на скачивание
к нам за прошлый год