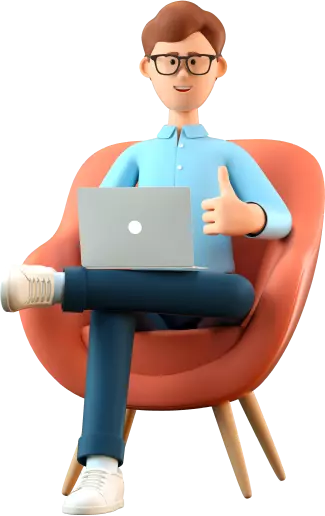
на первый
заказ
Решение задач на тему: 83972
Введение
Глава 1. Основные понятия надёжности технических систем……………..1.1.Понятие надежность технических систем………………………………
1.2. Показатели надежности…………………………………………………
1.3. Классификация отказов…………………………………………………
Глава 2. Методы анализа надежности и риска……………………………
Глава 3. Расчёт структурной схемы надёжности…………………………
Заключение………………………………………………………………….
Список использованной литературы……………………………………..
3.на основе продуктивной системы выявить условия обеспечивающие надежность технических систем.
Объект исследования: направления совершенствования расчетных методов надежности технических систем.
Предмет исследования: надежность технических систем.
Практическая значимость: выявление условий совершенствования расчетных методов надежности технических систем.
Методология исследования:
1.теоретический анализ совершенствования расчетных методов надежности технических систем;
2.наблюдение;
3.математические способы обработки данных.
Глава 1. Основные понятия надёжности технических систем
Глава 1.1. Понятие надежность технических систем
Первостепенное значение надёжности в технике связано с тем, что уровень надёжности в значительной степени определяет развитие техники по основным направлениям: по автоматизации производства, интенсификации рабочих процессов и транспорта, экономии материалов и энергии.
Современные технические средства состоят из множества взаимодействующих механизмов, аппаратов и приборов. Например, автоматизированные линии насчитывают более миллиона деталей. Отказ в работе хотя бы одного ответственного элемента такой системы может привести к нарушению работы всей линии.
Недостаточная надёжность оборудования приводит к огромным затратам на ремонт, простою оборудования, прекращению снабжения населения электроэнергией, водой, газом, транспортными средствами, невыполнению ответственных задач, иногда к авариям, связанным с большими экономическими потерями, разрушением крупных объектов и с человеческими жертвами.
Надёжность - это свойство объекта сохранять во времени в установленных пределах все параметры, обеспечивающие выполнение требуемых функций в заданных условиях эксплуатации[7].
В теории надёжности рассматриваются следующие обобщенные объекты (рис. 1):
1) изделие - единица продукции, выпускаемая данным предприятием, цехом и т. д.;
2) элемент - простейшая при данном рассмотрении составная часть изделия, в задачах надёжности может состоять из многих деталей;
3) система - совокупность совместно действующих элементов, предназначенная для самостоятельного выполнения заданных функций.
Рис. 1. Обобщенные объекты теории надежности
Понятия "элемент" и "система" трансформируются в зависимости от поставленной задачи. Машина, например, при установлении её собственной надёжности рассматривается как система, состоящая из отдельных элементов механизмов, деталей, и т. д., а при изучении надёжности автоматической линии как элемент[6].
Изделия подразделяют на невосстанавливаемые, которые не могут быть восстановлены потребителем и подлежат замене, например электрические лампы, микросхемы и т. д., и восстанавливаемые, которые могут быть восстановлены потребителем, например станок, автомобиль, радиоприемник (рис. 2).
Рис. 2. Невосстанавливаемые и восстанавливаемые изделия
Надёжность изделия характеризуется следующими основными состояниями:
1) работоспособность - состояние изделия, при котором оно способно нормально выполнять заданные функции;
2) исправность - состояние изделия, при котором оно удовлетворяет всем не только основным, но и вспомогательным требованиям.
Так, изделие может быть работоспособным, но неисправным, например, в работающем радиоприёмнике не освещён индикатор настройки. В свою очередь, исправное изделие обязательно работоспособно.
Неисправность - состояние изделия, при котором оно не соответствует хотя бы одному из требований технической документации.
Отказ - событие, заключающееся в полной или частичной утрате работоспособности[8].
Рассмотрим свойства изделий с точки зрения надёжности (рис. 3).
Рис. 3. Свойства изделий с позиции надежности
Надёжность изделий обусловливается их безотказностью, долговечностью, ремонтопригодностью и сохраняемостью [4].
Таким образом, надежность характеризуется свойствами, которые проявляются в эксплуатации и позволяют судить о том, насколько изделие оправдает надежды его изготовителя и потребителей.
Безотказность - свойство непрерывно сохранять работоспособность в течение заданного времени или наработки. Под наработкой понимают продолжительность или объём выполненной работы объекта. Это свойство особенно важно для машин, отказ в работе которых связан с опасностью для жизни людей или с перерывом в работе большого комплекса машин, с остановкой автоматизированного производства или с браком дорогого изделия[1].
Долговечность - свойство изделия длительно сохранять работоспособность до предельного состояния при установленной системе технического обслуживания и ремонтов.
Предельное состояние изделия характеризуется невозможностью его дальнейшей эксплуатации, снижением эффективности или безопасности. Для невосстанавливаемых изделий понятия "долговечность" и "безотказность" практически совпадают.
Ремонтопригодность - приспособленность изделия к предупреждению и обнаружению причин возникновения отказов, повреждений и поддержанию и восстановлению работоспособности путём технического обслуживания и ремонтов.
С усложнением систем всё сложнее становится находить причины отказов и отказавшие элементы. Так, в сложных электрогидравлических системах станков поиск причин отказа может занимать более 50 % общего времени восстановления работоспособности. Поэтому облегчение поиска отказавших элементов закладывается в конструкцию новых сложных автоматических систем. Важность ремонтопригодности машин определяется огромными затратами на ремонт машин в настоящее время[9].
Сохраняемость - свойство объекта сохранять значение показателей безотказности, долговечности и ремонтопригодности после хранения и транспортирования.
Практическая роль этого свойства особенно велика для приборов. Так, по американским источникам, во время второй мировой войны около 50 % радиоэлектронного оборудования для военных нужд и запасных частей к нему вышло из строя в процессе хранения.
Глава 1.2. Показатели надежности
Надёжность изделий в зависимости от их вида может оцениваться одним или несколькими показателями: безотказности, долговечности, ремонтопригодности и сохраняемости [5].
Показатели безотказности
Показатели безотказной работы представлены на рис. 4.
Рис. 4. Показатели безотказной работы
Вероятность безотказной работы - вероятность того, что в пределах заданной наработки отказ не возникнет. Под наработкой понимают продолжительность или объём выполненной работы объекта.
Средняя наработка до отказа - математическое ожидание наработки до отказа невосстанавливаемого изделия.
Средняя наработка на отказ - отношение наработки восстанавливаемого объекта к математическому ожиданию числа его отказов в течение этой наработки[11].
Интенсивность отказов - показатель надёжности невосстанавливаемых изделий, равный отношению среднего числа отказавших в единицу времени объектов к числу объектов, оставшихся работоспособными. Этот показатель более чувствителен, чем вероятность безотказной работы, особенно для изделий высокой надёжности.
Параметр потока отказов - показатель надёжности восстанавливаемых изделий, равный отношению среднего числа отказов восстанавливаемого объекта за произвольную малую его наработку к значению этой наработки.
Показатели долговечности[10].
Показатели безотказной работы представлены на рис. 5.
Рис. 5. Показатели долговечности
Ресурс - это наработка изделия до предельного состояния, оговоренного в технической документации. Другими словами, ресурс это чистое время работы изделия без учета остановок. Различают ресурс до первого ремонта, межремонтный ресурс, назначенный ресурс, гамма-процентный ресурс и т. д.
Назначенный ресурс - это наработка изделия, при достижении которой эксплуатация должна быть прекращена независимо от состояния изделия. Назначенный ресурс указывается в техдокументации из соображения безопасности и экономичности. Назначенный ресурс может выражаться различными величинами: часами работы (например, для двигателей), количеством выстрелов (для орудий), километрами пробега и т. д. Назначение ресурса обязательно для авиационной, военной и космической техники. В настоящее время аналогичное понятие всё шире внедряется во все отрасли техники в виде гарантированного ресурса, который предприятие-изготовитель
гарантирует заказчику[13].
Гамма-процентный ресурс - ресурс, который имеет и превышает в среднем обусловленное число процентов изделий данного типа.
Срок службы - календарная продолжительность эксплуатации изделия до момента возникновения предельного состояния, оговоренного в технической документации или до списания. Различают срок службы до среднего ремонта, капитального ремонта, между капитальными ремонтами, средний срок службы, срок службы до списания и др. Ресурс работы является частью срока службы и выражает чистое время работы машины.
Срок гарантии - период, в течение которого изготовитель гарантирует и обеспечивает выполнение установленных требований к изделию при условии соблюдения потребителем правил эксплуатации, в том числе правил хранения и транспортировки. Срок гарантии устанавливается в технической документации при договорах между изготовителем и заказчиком[15].
Глава 1.3. Классификация отказов
Отказы, являющиеся неотъемлемым свойством изделия, могут быть классифицированы по ряду признаков [2]. Рассмотрим некоторые из них (рис. 6).
По значимости отказы бывают критическими, существенными и несущественными.
Критический отказ - это отказ изделия, при котором появляется угроза человеку или окружающей среде.
Существенный отказ характеризуется тем, что значительное снижение эксплуатационных характеристик или полная непригодность изделия не связаны с опасностью для человека.
Несущественный отказ вызывает только неудовольствие, последствия его незначительны[17].
По характеру возникновения различают внезапные, постепенные и систематические отказы.
Внезапный отказ - это отказ, характеризующийся скачкообразным изменением одного или нескольких заданных параметров объекта. Внезапные отказы возникают в результате сочетания неблагоприятных факторов и случайных внешних воздействий, превышающих возможности изделия. Основным признаком внезапного отказа является независимость вероятности его возникновения в течение заданного периода времени от длительности предыдущей работы изделия[19].
Постепенный отказ - отказ, связанный с постепенным изменением значения одного или нескольких заданных параметров объекта. Постепенные (их называют износными) отказы возникают в результате протекания процесса старения, ухудшающего начальные параметры изделия.
Рис. 6. Классификация отказов
Систематический отказ - многократно повторяющийся и однородный по определенным признакам отказ, обусловленный дефектами конструкции объекта, нарушением процесса его изготовления, низким качеством используемых материалов и т. д. Причина возникновения систематического отказа может быть установлена и устранена.
По характеру обнаруживаемости отказы делят на явные и скрытые.
Явный отказ - это отказ, появление которого сопровождается признаками, непосредственно воспринимаемыми органами чувств наблюдателя или средствами контроля, без проведения дополнительных операций по контролю работоспособности объекта[21].
Скрытый отказ - отказ, обнаружение которого невозможно без проведения специальных операций по контролю работоспособности объекта.
По причине возникновения различают отказы конструкционные, технологические и эксплуатационные.
Конструкционный отказ - отказ, возникающий в результате несовершенства или нарушения установленных параметров при конструировании изделия.
Технологический отказ вызывается несовершенством или нарушением технологии.
Эксплуатационный отказ происходит из-за неправильной эксплуатации изделия.
По характеру работы после возникновения отказа различают отказы функционирования и параметрические отказы.
Отказ функционирования - это отказ, при наступлении которого изделие перестает выполнять свои функции. Дальнейшая эксплуатация возможна только после ремонта.
Параметрический отказ - это отказ, характеризующийся отклонением значения хотя бы одного рабочего параметра машины за пределы допуска. Продолжение эксплуатации машины, имеющей такой отказ, может привести к выпуску некачественной продукции или к снижению эффективности работы машины. Более того, в сложных машинах и системах параметрические отказы
элементов могут привести к отказу функционирования[24].
По возможности устранения причин отказа различают неустранимые отказы и устранимые.
Неустранимый отказ - это отказ, причины которого неизвестны или не могут быть устранены для изделия данного вида.
Устранимый отказ - это отказ, причины возникновения которого известны и могут быть полностью устранены, что исключит их возникновение при дальнейшем существовании объектов данного вида.
По характеру устранения различают устойчивые отказы, самоустраняющиеся отказы, сбой и перемежающиеся отказы.
Устойчивый отказ - это отказ, для устранения которого необходимо проводить специальную работу.
Самоустраняющийся отказ - отказ, приводящий к кратковременному нарушению работоспособности объекта.
Сбой - отказ, не нарушающий работоспособности объекта, приводит лишь к кратковременной потере или искажению полезной информации в системе.
Перемежающийся отказ - многократно возникающий самоустраняющийся отказ объекта одного и того же характера.
По времени возникновения отказы делят на приработочные, возникающие в первый период эксплуатации и связанные с выявлением дефектных элементов, не отбракованных контролем, при нормальной эксплуатации и износовые[27].
Глава 2. Методы анализа надежности и риска
Чтобы эффективно управлять риском, его необходимо проанализировать и оценить. Анализ риска служит полезным средством, когда имеется намерение выявить существующие опасности, определить уровни рисков выявленных нежелательных событий (по частоте и последствиям) и реализовать меры по уменьшению риска в случае превышения его приемлемого уровня.
Методы анализа надежности и риска могут быть не только количественными, при которых основные результаты получаются путем расчета показателей надежности и риска, но и качественными, при которых результаты представлены в виде текстового описания, таблиц, диаграмм путем применения качественных методов анализа отказов, опасностей и экспертных оценок [3].
При выборе методов анализа надежности и риска необходимо учитывать этап разработки системы, цели анализа, критерии приемлемого риска, тип анализируемой системы и характер опасности, наличие ресурсов для проведения анализа необходимой информации, опыт и квалификацию исполнителей и другие факторы.
Метод анализа надежности и риска должен удовлетворять следующим требованиям:
- быть научно обоснованным и соответствовать рассматриваемой системе;
- давать результаты в виде, позволяющем лучше понимать характер отказов и риска и намечать пути его снижения;
- быть повторяемым и проверяемым.
Ниже представлены основные методы, используемые при проведении анализа надежности и риска.
Методы "Проверочного листа" и "Что будет, если…?"
Методы "Проверочного листа" и "Что будет, если…?" или их комбинации относятся к группе качественных методов оценки надежности и риска, основанных на изучении соответствия условий эксплуатации объекта или проекта действующим требованиям промышленной безопасности[30].
Результат "Проверочного листа" - перечень вопросов и ответов о соответствии объекта требованиям надежности и безопасности и указания по обеспечению надежности и безопасности. Метод "Проверочного листа" отличается от метода "Что будет, если...?" более обширным представлением исходной информации и результатов о последствиях отказов, нарушений безопасности. Эти методы наиболее просты (особенно при обеспечении их вспомогательными формами, унифицированными бланками, облегчающими на практике проведение анализа и представление результатов), недороги (результаты могут быть получены одним человеком в течение одного дня) и наиболее эффективны при исследовании надежности и безопасности хорошо изученных объектов с известной технологией или объектов с незначительным риском крупной аварии.
Метод "Анализ вида и последствий отказов" (АВПО)
Метод "Анализ вида и последствий отказов" (АВПО) применяется для качественной оценки надежности и риска технических систем. Существенной чертой этого метода является рассмотрение каждого аппарата (установки, блока, изделия) или составной части системы (элемента) на предмет того, как он стал неисправным (вид и причина отказа) и как этот отказ воздействует на техническую систему (последствия отказа). "Анализ вида и последствий отказа" можно расширить до "Количественного анализа вида, последствий и критичности отказа" (АВПКО).
В этом случае каждый вид отказа ранжируется с учетом двух составляющих критичности - вероятности (или частоты) и тяжести последствий отказа. Понятие критичности близко к понятию риска и может быть использовано при более деталь- ном количественном анализе риска аварии. Определение пара метров критичности необходимо для выработки указаний и приоритетности мер безопасности.
Результаты анализа представляются в виде таблиц с перечнем оборудования, вида и причин возможных отказов, частоты, последствий, критичности, средств обнаружения неисправности (сигнализаторы, приборы контроля и т. п.) и рекомендаций по уменьшению опасности. В таблице 1 приведены рекомендуемые показатели (индексы) уровня и критерии критичности по вероятности и тяжести последствий отказа (события).
При анализе необходимо выделять четыре группы, которым может быть нанесен ущерб от аварии: персонал, население, окружающая среда, материальные объекты (оборудование и сооружения промышленного предприятия и близлежащих населенных пунктов). В таблице 1 приведены следующие критерии: критерии отказов по тяжести последствий:
1) катастрофический отказ - приводит к смерти людей, наносит существенный ущерб объекту и невосполнимый ущерб окружающей среде;
2) критический (некритический) отказ - угрожает (не угрожает) жизни людей, потере объекта, окружающей среде;
3) отказ с пренебрежимо малыми последствиями - не относящимися по своим последствиям ни к одной из первых трех категорий.
Категории отказов (степень риска отказа):
А - обязателен детальный анализ риска, требуются особые меры безопасности для снижения риска; В - желателен детальный анализ риска, требуются меры безопасности;
С - рекомендуется проведение анализа риска и принятие мер безопасности;
Д - анализ и принятие мер безопасности не требуются.
Таблица 1
Матрица "Вероятность-тяжесть последствий"
Тяжесть последствий
Ожидаемая частота возникновения (1/год)
Катастрофический отказ
Критический отказ
Некритический отказ
Отказ с пренебрежимо малыми последствиями
Частый отказ
С
Вероятный отказ
В
С
Возможный
отказ
В
В
С
Редкий отказ
В
С
Д
Практически
невероятный
отказ
В
С
С
Д
Критерии, приведенные в таблице 1, могут применяться для ранжирования опасности и определения степени риска всего промышленного объекта. В этом случае ранг А соответствует наиболее высокой (неприемлемой) степени риска объекта, требующей незамедлительных мер по обеспечению безопасности.
Соответственно показатели В, С отвечают промежуточным степеням риска, а ранг Д - наиболее безопасным условиям. Проблема заключается в учете вкладов рисков неполадок (отказов) составных частей промышленного объекта в общий риск аварии. Методы АВПО, АВПКО применяются для анализа проектов сложных технических систем или при модификации опас-
ных производств.
Метод "Анализ опасности и работоспособности" (АОР)
В методе "Анализ опасности и работоспособности" (АОР) исследуется влияние отклонений технологических параметров (температуры, давления и др.) от регламентных режимов с точки зрения возникновения отказов и опасности. АОР по сложности и качеству результатов соответствует уровню АВПО, АВПКО.
В процессе анализа для каждой производственной линии и блока определяются возможные отклонения, причины и указания по их недопущению. При характеристике отклонения используются ключевые слова: "НЕТ", "БОЛЬШЕ", "МЕНЬШЕ", "ТАК ЖЕ, КАК", "ДРУГОЙ", "ИНАЧЕ, ЧЕМ", "ОБРАТНЫЙ" и т. п. Применение ключевых слов помогает исполнителям выявить все возможные отклонения. Конкретное сочетание этих
слов с технологическими параметрами определяется спецификой производства.
Примерное содержание ключевых слов следующее:
- НЕТ - отсутствие прямой подачи вещества, когда она должна быть;
- БОЛЬШЕ (МЕНЬШЕ) - увеличение (уменьшение) значений режимных переменных, по сравнению с заданными (температуры, давления, скорости потока);
- ТАК ЖЕ, КАК - появление дополнительных компонентов (воздух, вода, примеси);
- ДРУГОЙ - состояние, отличающееся от обычной работы установки (пуск, остановка, повышение производительности и т. д.);
- ИНАЧЕ, ЧЕМ - полное замещение процесса, непредвиденное событие, разрушение, разгерметизация оборудования;
- ОБРАТНЫЙ - логическая противоположность замыслу, появление обратного потока вещества.
Результаты анализа представляются на специальных технологических листах (таблицах). Степень опасности отклонений может быть определена количественно путем оценки вероятности и тяжести последствий рассматриваемой ситуации по критериям критичности аналогично методу АВПКО (таблица 1).
Отметим, что метод АОР так же, как АВПКО, кроме идентификации отказов и опасностей и их ранжирования, позволяет выявить неясности и неточности в инструкциях по безопасности и способствует их дальнейшему совершенствованию. Недостатки методов связаны с затрудненностью их применения для анализа комбинаций событий, приводящих к аварии.
Логико-графические методы анализа
"Дерева отказов и событий". Практика показывает, что возникновение и развитие крупных аварий, как правило, характеризуется комбинацией случайных локальных событий, возникающих с различной частотой на разных стадиях аварии (отказы оборудования, человеческие ошибки, внешние воздействия, разрушение, выброс, пролив вещества, рассеяние веществ, воспламенение, взрыв, интоксикация и т. д.). Для выявления причинно-следственных связей между этими событиями используют логико-графические методы анализа "Дерева отказов и событий".
При анализе "Дерева отказов" выявляются комбинации отказов (неполадок) оборудования, ошибок персонала и внешних (техногенных, природных) воздействий, приводящих к основному событию (аварийной ситуации). Метод используется для анализа возможных причин возникновения аварийной ситуации и расчета ее частоты (на основе знания частот исходных
событий).
Основной принцип построения "Дерева отказов" состоит в последовательной постановке вопроса: по каким причинам может произойти нежелательное событие (авария, несчастный случай, отказ изделия), т. е. в осуществлении анализа сверху вниз.
Преимущества и недостатки метода анализа "Дерева отказов".
"Дерево отказов" представляет собой многоуровневую графологическую структуру причинных взаимосвязей, полученных в результате прослеживания опасных ситуаций в обратном порядке, для того чтобы отыскать возможные причины их возникновения (рис. 7.).
Рис. 7. Граф дерева отказов
Преимущества метода "Дерева отказов" заключаются в следующем:
- анализ ориентируется на нахождение отказов;
- позволяет показать в явном виде ненадежные места;
- обеспечивается графикой и представляет наглядный материал для той части работников, которые принимают участие в обслуживании системы;
- дает возможность выполнять качественный или количественный анализ надежности системы;
- метод позволяет специалистам поочередно сосредотачиваться на отдельных конкретных отказах системы;
- обеспечивает глубокое представление о поведении системы и проникновение в процесс ее работы;
- являются средством общения специалистов, посколькутони представлены в четкой наглядной форме;
- помогает дедуктивно выявлять отказы;
- дает конструкторам, пользователям и руководителя возможность наглядного обоснования конструктивных изменений или установления степени соответствия конструкции системы заданным требованиям и анализа компромиссных решений;
- облегчает анализ надежности сложных технических систем.
Главное преимущество метода "Дерева отказов" (по сравнению с другими методами) заключается в том, что анализ ограничивается выявлением только тех элементов системы и событий, которые приводят к данному конкретному отказу системы или аварии.
Недостатки метода "Дерева отказов":
- реализация метода требует значительных затрат средств и времени;
- "Дерево отказов" представляет собой схему булевой логики, на которой показывают только два состояния: рабочее и отказавшее состояние;
- трудно учесть состояние частичного отказа элементов, поскольку при использовании метода, как правило, считают, что система находится либо в исправном состоянии, либо в состоянии отказа;
- трудности в общем случае аналитического решения для "деревьев", содержащие резервные узлы и восстанавливаемые узлы с приоритетами, не говоря уже о тех значительных усилиях, которые требуются для охвата всех видов множественных отказов; - требует от специалистов по надежности глубокого понимания системы и конкретного рассмотрения каждый раз только
одного определенного отказа;
- "Дерево отказов" описывает систему в определенный момент времени (обычно в установившемся режиме), и последовательности событий могут быть показаны с большим трудом, иногда это оказывается невозможным. Это справедливо для систем, имеющих сложные контуры регулирования.
Основные блоки дерева отказов. Чтобы отыскать и наглядно представить причинную взаимосвязь с помощью "Дерева отказов" используются два типа элементарных блоков: логические символы и символы событий.
Логические символы связывают события в соответствии с их причинными взаимосвязями. Обозначения их приведены в таблице 2. Символы событий даны в таблице 3.
Использование блоков дерева. Рассмотрим принцип определения вероятностей вершинных отдельных ветвей событий, использующих наиболее распространенные логические символы. На рис. 8 приведена иллюстрация использования при работе логического символа "И".
При расчетах вероятности события, соединенные условием "И", перемножаются. Так, вероятность события А в зависимости от исходных
событий 1,2,…., n, вероятности которых Р1, Р2,… , Рn будут определяться по формуле
Вероятность события А, в зависимости от исходных событий, соединенных символом "ИЛИ", определяется по формуле
В частности, при n = 2 выражение преобразуется к виду
Таблица 2
Логические символы
Символ логического знака
Название логического знака
Причинная взвимосвязь
Выходное событие происходит, если все входные события случаются одновременно
"ИЛИ"
Выходное событие происходит, если случается любое из входных событий
"ЗАПРЕТ"
Наличие входа вызывает появление выхода тогда, когда происходит условное событие
Приоритетное "И"
Выходное событие имеет место, если все входные события происходят в нужном порядке слева направо
Исключающее
"ИЛИ"
Выходное событие происходит, если случается одно (но не оба) из входных событий
"m из n"
Выходное событие происходит, если случается "m" из "n" входных событий
Таблица 3
Символы событий
Символ события
Содержание события
Исходное событие, обеспеченное достаточными данными
Событие, недостаточно детально разработанное
Событие, вводимое логическим элементом
Условное событие, используемое с логическим знаком "запрет"
Событие, которое может случаться или не случаться
Символ перехода
Выходное событие логического символа "И" наступает в том случае, если все входные события появляются одновременно.
Правило формулирования событий. События, входные по отношению к операции "И", должны формулироваться так, чтобы второе было условным по отношению к первому, третье условным по отношению к первому и второму, а последнее - условным ко всем предыдущим. Кроме того, по крайней мере, одно из событий должно быть связано с появлением выходного события.
Рис. 8. Применение логического символа "И"
Рис. 9. Применение логического символа "ИЛИ"
Полная характеристика события не требуется. Иногда она даже мешает графической ясности диаграммы. Требуется лишь упорядочить события так, чтобы стоящее справа зависело от появления стоящего слева. Таким образом, появление выходного события будет определяться появлением последнего события в ряду n-событий.
Правило применения логического символа "И". Если имеются несколько причин, которые должны появиться одновременно, то обычно используют операцию "И". Входы операции должны отвечать на вопрос: "Что необходимо для появления выходного события?".
Выходное событие логического символа "ИЛИ" наступает в том случае, если имеет место любое из входных событий.
Правило формулирования событий. События, входные по отношению к операции "ИЛИ", должны формулироваться так, чтобы они вместе исчерпывали все возможные пути появления выходного события. Кроме того, любое из входных событий должно приводить к появлению выходного события.
Правило не дает способа описания событий, но оно должно выполняться при построении "Дерева отказа".
Правило применения логического символа "ИЛИ". Если любая из причин приводит к появлению выходного события, следует использовать операцию "ИЛИ". Входы операции отвечают на вопрос: "Какие события достаточны для появления выходного события?". Порядок применения логических символов "И" и "ИЛИ". Для любого события, подлежащего дальнейшему анализу, вначале рассматриваются все возможные события, являющиеся входами операций "ИЛИ", затем входы операций "И". Это справедливо как для головного события, так и для любого события, анализ которого целесообразно продолжить.
Событие "Возникновение пожара" имеет место, если два события: "Утечка горючей жидкости" "И" "Очаг воспламенения вблизи горючей жидкости", происходят одновременно. Последнее (критическое) событие случается, если происходит одно из двух событий - "Наличие искры" "ИЛИ" "Курящий рабочий".
Последовательность построения "Дерева отказов". Построение "Дерева отказов" и анализ исследуемого объекта с его использованием производят следующим образом.
1. Определяют аварийное (предельно опасное, конечное) событие, которое образует вершину "дерева". Данное событие четко формулируют, оговаривают условия его появления, дают признаки его точного распознания. Например, для объектов химической технологии к таким событиям относятся: разрыв аппарата, пожар, выход реакции из-под контроля и др. Определяют
возможные первичные и вторичные отказы, которые могут вызвать головное событие, рассматривают их комбинации.
Рис. 10. Пример использования логических символов "И" и "ИЛИ"
2. Используя стандартные символы событий и логические символы (табл. 7.2, 7.3), "дерево" строят в соответствии со следующими правилами:
а) конечное (аварийное) событие помещают вверху;
б) "дерево" состоит из последовательности событий, которые ведут к конечному событию;
в) последовательности событий образуются с помощью логических знаков "И", "ИЛИ" и др.;
г) событие над логическим знаком помещают в прямоугольнике, а само событие описывают в этом прямоугольнике;
д) первичные события (исходные причины) располагают
снизу "дерева".
3. Квалифицированные эксперты проверяют правильность построения "дерева". Это позволяет исключить субъективные ошибки разработчика, повысить точность и полноту описания объекта и его действия.
4. Определяют минимальные аварийные сочетания и минимальную траекторию для построенного "дерева". Первичные и неразлагаемые события соединяются с событиями первого уровня маршрутами (ветвями). Сложное "дерево" имеет различные наборы исходных событий, при которых достигается событие в вершине, они называются аварийными сочетаниями (сечениями) или прерывающими совокупностями событий. Минимальным аварийным сочетанием (МАС) называют наименьший набор исходных событий, при которых возникает событие в вершине. Полная совокупность МАС "дерева" представляет собой все варианты сочетаний событий, при которых может возникнуть авария (отказ или иное нежелательное событие). Минимальная траектория - наименьшая группа событий, при появлении которых происходит авария.
5. Качественно и количественно исследуют "дерево" отказов (аварий) с помощью выделенных минимальных аварийных сочетаний и траекторий. Качественный анализ заключается в сопоставлении различных маршрутов и начальных событий к конечному и определении критических (наиболее опасных) путей, приводящих к аварии. При количественном исследовании
рассчитывают вероятность появления аварии в течение задаваемого промежутка времени по всем возможным маршрутам.
6. Разрабатывают рекомендации по введению изменений в объекте, системах контроля и управления для улучшения показателей безаварийности.
Анализ "Дерева событий" - алгоритм построения последовательности событий, исходящих из основного события (аварийной ситуации). Используется для анализа развития аварийной ситуации. Частота каждого сценария развития аварийной ситуации рассчитывается путем умножения частоты основного события на вероятность конечного события (например, аварии с разгерметизацией аппарата с пожаровзрывоопасным веществом в зависимости от условий могут развиваться как с воспламенением, так и без воспламенения вещества).
Методы "Дерева отказов и событий" трудоемки и применяются, как правило, для анализа проектов или модернизации сложных технических систем и производств.
Методы количественного анализа надежности и риска.
Методы количественного анализа надежности и риска характеризуются расчетом показателей надежности и риска и могут включать один или несколько вышеупомянутых методов (или использовать их результаты). Проведение количественного анализа требует высокой квалификации исполнителей, большого объема информации по аварийности, надежности оборудования, учета особенностей окружающей местности, метеоусловий, времени пребывания людей на территории и вблизи объекта, плотности населения и других факторов.
Количественный анализ надежности и риска наиболее эффективен:
- на стадии проектирования и размещения опасных установок и объектов;
- при оценке безопасности объектов, имеющих однотипное оборудование (например, магистральные трубопроводы);
- при необходимости получения комплексной оценки воздействия аварий на людей, материальные объекты и окружающую природную среду;
- при разработке приоритетных мер по подготовке к чрезвычайным ситуациям в регионе, насыщенном опасными промышленными объектами.
Недостатками количественного анализа надежности и риска являются невысокая точность результатов, вследствие чего использование количественных показателей (в частности, вероятности возникновения аварии) в качестве критериев безопасности для сложных производств, как правило, не оправдано.
Глава 3. Расчёт структурной схемы надёжности
Для расчёта структурной схемы надёжности используем процесс производства многослойных неглазированных конфет с валковыми формующими механизмами, представленный на рисунке 11.
Рис. 11. - Схема производства многослойных неглазированных конфет с валковыми формующими механизмами
1 - движущаяся конвейерная лента; 2, 5, 6 - формующие механизмы; 3, 4 - смесители; 7 - охлаждающая камера; 8 - дисковые ножи; 9 - резательная машина непрерывного действия; 10 - гильотинный нож; 11 - трехъярусный ленточный конвейер.
После тщательного перемешивания массы смеситель 3 опрокидывается и масса по трубопроводам поступает в приемные воронки формующих механизмов 2 и 6.
Аналогично из смесителя 4 масса подается в воронку формующего механизма 5.
Формование бесконечного конфетного пласта на движущейся конвейерной ленте 1 осуществляется валковыми формующими механизмами, имеющими по два гладких вращающихся навстречу друг другу валка. Длина валков 500 мм, диаметр 2
Оглавление
- Ведениеили зарегистрироваться
в сервисе
удобным
способом
вы получите ссылку
на скачивание
к нам за прошлый год