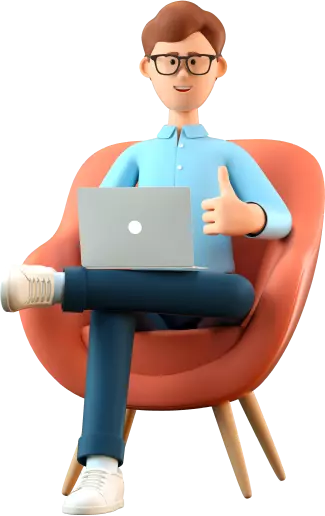
на первый
заказ
Дипломная работа на тему: Основы порошковой металлургии. Способы получения и технологические свойства порошков
Купить за 600 руб.Введение
Порошковыми называют материалы, изготовляемые путем прессования металлических порошков в изделия необходимой формы и размеров и последующего спекания сформованных изделий в вакууме или защитной атмосфере при температуре 0,75-0,8ТПЛ. Различают пористые и компактные порошковые материалы.Пористыми называют материалы, в которых после окончательной обработки сохраняется 10-30% остаточной пористости. Эти сплавы используют главным образом для изготовления антифрикционных деталей (подшипников, втулок) и фильтров.
Антифрикционные порошковые сплавы имеют низкий коэффициент трения, легко прирабатываются, выдерживают значительные нагрузки и обладают хорошей износостойкостью.
Подшипники из порошковых сплавов могут работать без принудительного смазывания за счет "выпотевания" масла, находящегося в порах.
Подшипники изготовляют из сплавов железа и 1-7% графита (ЖГр1, ЖГрЗ, ЖГр7) и бронзографита, содержащего 8-10% Sn и 2-4% графита (БрОГр10-2, БрОГр8-4 и др.).
Структура металлической основы железографитовых материалов должна быть перлитной, с массовой долей связанного углерода ~1,0%. Такая структура допускает наиболее высокие скорости и нагрузки при наименьшем износе подшипников. Добавка к железографитовым материалам серы (0,8-1,0%) или сульфидов (3,5-4,0%), образующих сульфидные пленки на трущихся поверхностях, улучшает прирабатываемость, уменьшает износ и прихватываемость сопряженных деталей.
Коэффициент трения железографита по стали при смазке 0,07-0,09. Подшипники из железографита применяют при допустимой нагрузке не более 1000-1500 МПа и максимальной температуре 100-200°С. Коэффициент трения бронзографита по стали без смазывания 0,04-0,07 и со смазыванием 0,05-0,007. Допустимая нагрузка 400-500 МПа и рабочая температура не выше 200-250°С.
Механические свойства железографита: σВ=180÷300 МПа и твердость 60-120 НВ, а бронзиграфита: σВ=30÷50 МПа, твердость 25-50 НВ.
Спеченные материалы на основе железа и меди используют и для фрикционных изделий (дисков, сегментов) в тормозных узлах. Фрикционные изделия должны иметь высокий коэффициент трения, достаточную механическую прочность и хорошее сопротивление износу. Для повышения коэффициента трения в состав фрикционных материалов вводят карбиды кремния, бора, тугоплавкие оксиды и т.д. Компонентами твердого смазочного материала служат графит, свинец, сульфиды и др.
Коэффициент трения по чугуну (трение без смазочного материала) для материала на железной основе составляет 0,18-0,40, а на медной основе - 0,17-0,25.
Фрикционные сплавы на медной основе применяют для условий жидкостного трения в паре с закаленными стальными деталями (сегменты, диски сцепления и т.д.) при давлении до 400 МПа и скорости скольжения до 40 м/с с максимальной температурой 300-350°С. Типичным фрикционным материалом на основе меди является сплав МК5, содержащий 4% Fе, 7% графита, 8% Рb, 9% Sn, 0-2% Ni.
Для работы в условиях трения без смазочного материала (деталей тормозов самолетов, тормозных накладок тракторов, автомобилей, дорожных машин, экскаваторов и т.д.) применяют материалы на железной основе. Наибольшее применение получил материал ФМК-11 (15% Сu, 9% графита, 3% асбеста, 3% SiO2 и 6% барита), фрикционные материалы изготовляют в виде тонких секторов (сегментов, полос) и крепят на стальной основе (для упрочнения).
Широко применяют порошковые материалы для фильтрующих изделий. Фильтры в виде втулок, труб, пластин из порошков Ni, Fе, Тi, Аl, коррозионно-стойкой стали, бронзы и других материалов g пористостью 45-50% (размер пор 2-20 мкм) используют для очистки жидкостей и газов от твердых примесей.
В электротехнике и радиотехнике применяют порошковые магниты на основе Fе-Ni-А1-сплава (типа алнико) и др. Свойства порошковых магнитов нередко выше свойств литых магнитов.
Большое применение в машинах для контактной сварки, приборах связи получили контакты из порошковых материалов. Для этой цели применяют псевдосплавы тугоплавких металлов (W и Мо) с медью (МВ20, МВ40, MB60, MB80), серебром (СМ30, СМ60, СМ80, СВ30, СВ50, СВ85 и др.) или с оксидом кадмия (ОК8, ОК12, ОК15) и др. Контакты отличаются высокой прочностью, электропроводимостью и электроэрозионной стойкостью. Токосъемники (щетки) изготовляют из порошков меди (или серебра) с графитом (углем).
Все больше порошковая металлургия применяется для изготовления специальных сплавов: жаропрочных на никелевой основе, дисперсионно-упрочненных материалов на основе Ni, Аi, Тi и Сr. Методом порошковой металлургии получают различные материалы на основе карбидов W, Мо и Zr.
Спеченные алюминиевые сплавы (САС) применяют тогда, когда путем литья и обработки давлением трудно получить соответствующий сплав. Изготовляют CAC с особыми физическими свойствами. САС содержат большое количество легирующих элементов (например, САС1: 25-30% Si, 5-7% Ni, остальное Аl). Из САС1 делают детали приборов, работающих в паре со сталью при температуре 20-200°С, которые требуют сочетания низкого коэффициента линейного расширения и малой теплопроводности.
В оптико-механических и других приборах применяют высокопрочные порошковые сплавы системы А1-Zn-Мg-Си (ПВ90, ПВ90Т1 и др.). Эти сплавы обладают высокими механическими свойствами, хорошей обрабатываемостью резанием и релаксационной стойкостью. Изделия из этих сплавов подвергают термической обработке по режимам Т1 и Т2 (см. с. 396).
Применяют гранулированные специальные сплавы с высоким содержанием Fе, Ni, Со, Мn, Сr, Zr, Тi, V и других элементов, мало растворимых в твердом алюминии. Гранулы - литые частицы диаметром от десятых долей до нескольких миллиметров. При литье центробежным способом капли жидкого металла охлаждаются в воде со скоростью 104-106°С/с, что позволяет получить сильно пересыщенные твердые растворы переходных элементов в алюминии. При последующих технологических нагревах (400-450°С) происходит распад твердого раствора с образованием дисперсных фаз, упрочняющих сплав.
Все более широкое применение получают компактные материалы (1-3% пористости) из порошков углеродистой и легированной стали, бронз, латуней, сплавов алюминия и титана для изготовления всевозможных шестерен, кулачков, кранов, корпусов подшипников, деталей автоматических передач и других деталей машин.
Изготовляют большое количество порошковых конструкционных (СП10-1 ... СП10-4, СП30-1 ... СП30-4, СП30Д3-2, СП60Н2Д2-2, СП30Н3М-2, СП40Х-2, СП45Х3-2 и др.), мартенситно-стареющих (СПН12К5М5Г4ТЮ, СПН12Х5М3Т и др.), коррозионно-стойких (СПХ17Н2, СПХ18Н15, СПХ23Н28 и др.) и других сталей. В маркировке сталей добавочно введены буква "С", которая указывает класс материала - сталь, и буква "П" - порошковая. Цифра после дефиса показывает плотность стали в процентах. Стали подвергают термической обработке.
Свойства сталей, полученных из порошков после термической обработки, во многих случаях уступают свойствам сталей, полученных обычными металлургическими методами. Механические свойства порошковой стали зависят от плотности и содержания кислорода. При пористости более 3% заметно уменьшаются σВ, σ0,2, KCU, а порог хладноломкости t50 повышается даже при увеличении пористости более 2%. С повышением содержания кислорода более 0,01% снижается KCU и повышается t50.
Поэтому рекомендовать порошковую технологию для высоконагруженных стальных деталей нельзя. Вследствие более низких механических свойств, высокой стоимости исходного материала и энергоемкости процесса спекания порошковая конструкционная сталь может быть использована только для изготовления мало нагружаемых изделий, главным образом сложной формы.
Сплавы на основе цветных металлов (АЛП-2, АЛПД-2-4, АЛПЖ12-4, БрПБ-2, БрПО10-2, БрПО10Ц3-3, ЛП58Г2-2 и др.) нашли широкое применение в приборостроении электротехнической промышленности и электронной технике. В марке сплавов первые буквы, указывают класс материала ("Ал" - алюминий, "Б" - берилий, "Бр" - бронза, "Л" - латунь и т.д.), буква "П" - порошковый сплав и число после дефиса - плотность материала в процентах. Буквы ("Д" - медь, "Ж" - железо, "Г" - марганец и др.) и цифры в марке указывают состав сплава. Так же как обычные сплавы, порошковые сплавы на основе цветных металлов обладают высокой теплопроводностью и электропроводимостью, коррозионной стойкостью, немагнитны, хорошо обрабатываются резанием и давлением.
Порошковая металлургия позволяет увеличить коэффициент использования металла и повысить производительность труда.
Экономическая эффективность достигается благодаря сокращению или полному исключению механической обработки. Вследствие высокой стоимости пресс-форм изготовление деталей машин методами порошковой металлургии эффективно только в массовом производстве.
Применение порошковых материалов рекомендуется при изготовлении деталей простой симметричной формы (цилиндрические, конические, зубчатые), малых массы и размеров. Конструктивные формы детали не должны содержать отверстий под углом к оси заготовки, выемок, внутренних полостей и выступов. Конструкция и форма детали должны позволять равномерно заполнять полость пресс-формы порошками, их уплотнение, распределение напряжений и температуры при прессовании и удалении изделия из пресс-формы.
Оглавление
- Основы порошковой металлургии- Способы получения и технологические свойства порошков
- Металлокерамические материалы
- Конструкционные порошковые материалы
- Изготовление металлокерамических деталей
- Приготовление смеси
- Способы формообразования заготовок и деталей
- Спекание и окончательная обработка заготовок
- Технологические требования, предъявляемые к конструкциям деталей из металлических порошков
- Композиционные материалы с металлической матрицей
- Волокнистые композиционные материалы
- Дисперсно-упрочненные композиционные материалы
- Композиционные материалы с неметаллической матрицей
- Общие сведения, состав и классификация
- Карбоволокниты
- Карбоволокниты с углеродной матрицей
- Бороволокниты
- Органоволокниты
- Литература 18
- Основы порошковой металлургии
- Способы получения и технологические свойства порошков Металлокерамика, или порошковая металлургия - отрасль технологии, занимающаяся производством металлических порошков и деталей из них. Сущность порошковой металлургии заключается в том, что из металлического порошка или смеси порошков прессуют заготовки, которые затем подвергают термической обработке - спеканию
- Порошковой металлургией можно получать детали из особо тугоплавких металлов, из нерастворимых друг в друге металлов вольфрам и медь, железо и свинец и т. д., пористые материалы и детали из них, детали, состоящие из двух биметаллы или нескольких слоев различных металлов и сплавов
- Металлические порошки состоят из очень мелких частиц 0,5-500 мкм различных металлов и их окислов. Порошки получают механическим и физико-химическим путем
- Для механического измельчения твердых и хрупких материалов применяют шаровые, вибрационные мельницы и бегуны. Порошки из пластичных и легкоплавких металлов и сплавов получают различными способами, основанными на раздуве жидкого материала струей воды или газа. Механическим путем, как правило, получают порошки из отходов основного производства
- К физико-химическим способам получения порошков относят восстановление окислов металлов, электролиз и др
- Окислы металлов можно восстанавливать газообразными или твердыми восстановителями. Наибольшее практическое применение нашли газообразные углеродистые и углеводородистые соединения природный газ, доменный, углекислый газ и водород. Электролизом водных растворов солей получают тонкие и чистые порошки различных металлов и сплавов. Порошки из редких металлов тантала, циркония, титана и др. получают электролизом расплавленных солей. Режимы и технология изготовления порошков физико-химическим путем приведены в справочной литературе
- Основными технологическими свойствами порошков являются текучесть, прессуемость и спекаемость
- Текучесть - способность порошка заполнять форму. Текучесть ухудшается с уменьшением размеров частиц порошка и повышением влажности. Количественной оценкой текучести является скорость вытекания порошка через отверстие диаметром 1,5-4,0 мм в секунду
- Прессуемость характеризуется способностью порошка уплотняться под действием внешней нагрузки и прочностью сцепления частиц после прессования. Прессуемость порошка зависит от пластичности материала частиц, их размеров и формы и повышается с введением в его состав поверхностно-активных веществ
- Под спекаемостъю понимают прочность сцепления частиц в результате термической обработки прессованных заготовок
Список литературы
1. Гуляев А.П. "Металловедение", М.: 1968.2. Дальский А.М. "Технология конструкционных материалов", М.: 1985.
3. Куманин И.Б. "Литейное производство", М.: 1971.
4. Лахтин Ю.М. "Материаловедение", М.: 1990.
5. Семенов "Ковка и объемная штамповка", М.: 1972.
или зарегистрироваться
в сервисе
удобным
способом
вы получите ссылку
на скачивание
к нам за прошлый год